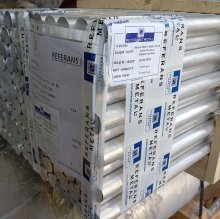
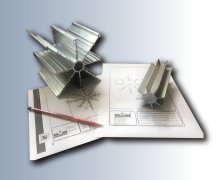
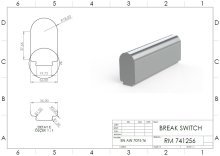
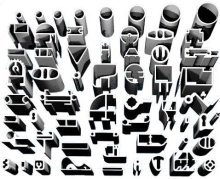
Plates
Sheets
Rod/Round Bar/Flat Bar
Tube/Extrusions/Profile
2014A
ASTM B210 / AlCu4SiMg / 2014A / T351
Chemical Properties | % Value |
Silicon (Si) | 0,50 - 0,90 |
Chromium (Cr) | 0,00 - 0,10 |
Manganese (Mn) | 0,40 - 1,20 |
Magnesium (Mg) | 0,20 - 0,80 |
Copper (Cu) | 3,90 - 5,00 |
Titanium (Ti) | 0,00 - 0,20 |
Iron (Fe) | 0,00 - 0,50 |
Zinc (Zn) | 0,00 - 0,25 |
Aluminium (Al) | Balance |
Titanium + Zirconium (Ti+Zr) | 0,00 - 0,20 |
Physical Properties | Value |
Density | 2.80 g/cm³ |
Melting Point | 510 °C |
Thermal Expansion | 22.8 µm/m.°C |
Modulus of Elasticity | 73 GPa |
Thermal Conductivity | 155 W/m.K |
Electrical Resistivity | 40% IACS |
Mechanical Properties | Value |
Proof Strength | 330 MPa |
Yield Strength | 430 MPa |
Shear Strength | 250 MPa |
Elongation A50 mm | 6.7 % |
Hardness | 120 HB |
2014A T351 aluminum alloy is a material known for its high strength, excellent machinability, and fatigue resistance. With its copper alloy content, this alloy offers enhanced mechanical performance, making it ideal for demanding applications requiring high strength and durability. The T351 temper indicates that the alloy has undergone solution heat treatment, stress-relief through mechanical processing, and natural aging for stability. These characteristics make it both reliable and robust.
This alloy is widely used in industries such as aerospace, automotive, military equipment, and industrial machinery. It is particularly favored for structural components, aircraft body parts, engine components, and chassis elements requiring high durability. 2014A T351 is compatible with anodizing, though careful control is necessary due to its copper content. Anodizing can enhance its corrosion resistance while providing an aesthetic surface. However, its weldability is limited, making mechanical fasteners or specialized welding techniques the preferred options.
In terms of bending and forming, 2014A T351 aluminum alloy provides moderate formability. Its high strength can make complex forming processes challenging, but with proper techniques, it can be successfully shaped. Its fatigue resistance and mechanical stability make it a reliable choice for high-vibration environments and applications subjected to dynamic loads. These properties ensure dependable performance in long-term use.
Corrosion resistance is moderate, so additional surface treatments or coatings are recommended for use in corrosive environments. Advantages of this alloy include high strength, excellent machinability, and fatigue resistance, while its disadvantages include limited weldability, reduced formability, and moderate corrosion resistance. These characteristics make 2014A T351 aluminum alloy an excellent choice for projects requiring lightweight materials with superior mechanical performance.
Cold Drawn Round/Flat Bars per : 2014A T351, ISO AlCu4SiMg, MIL-A-A21180, ASTM B211, UNS A92014, WNR 3.1255
Cold Drawn Tubes per; 2014A T351, ISO AlCu4SiMg, MIL-A-21180, ASTM B210, UNS A92014, WNR 3.1255
Choosing Factors for 2014A T351
- Strength: Exquisite
- Machining: Great
- Weldability: Bad
- Formability: Good
- Corrosion Resistance: Poor
- Heat Treating: Yes
Some Well-Known Applications for 2014A T351
In the automotive industry and defense industry,
In military vehicles and hydraulic applications,
It is also used in the automotive industry and as aircraft construction material.
- Plate/Sheet
- Rod / Round Bar / Flat Bar
- Tube/Profile
Mechanical Properties | |||
Thickness (mm) | Proof Strength (Min.) | Yield Strength (Min.) | Elongation A50 mm % |
Over 0.4 up to & incl. 0.8 | 370 MPa | 430 MPa | %6 |
Over 0.8 up to & incl. 1.6 | 380 MPa | 440 MPa | %7 |
Over 1,6 up to & incl. 6,0 | 390 MPa | 440 MPa | %7 |